*The period for calculating our environmental performance data is April to March, which is the same as the period covered by the report to submit to the government.
Prevention of Global Warming
Reduction of CO2 Emissions
Kagome was designated as a Specified Consigner*1 pursuant to the Act on the Rational Use of Energy that was revised in April 2006.
In FY2016, CO2 emissions from transportation and delivery of cargoes by Kagome increased approx. 0.8% from the FY2015 level, to 24,100 t-CO2. Emissions per unit of sales volume in terms of weight decreased approx. 2.3% year on year, to 44.3kg-CO2/t. In addition, while Specified Consigners are required to make efforts to reduce their specific energy consumption by an annual average of 1% or more in the medium and long runs, we reduced the emissions by an annual average of 1.1% during the five years from FY2012 to FY2016, which means we have been making improvements.
This is attributed in part to the start of joint delivery in the Hokkaido area in April 2016, with six manufacturers*2 participating in the F-LINE*3 project, and the use of rail for long-distance transportation, which increased with growth in sales.
We will continue to reduce CO2 emissions from transportation and delivery through measures such as increasing the rate of use of large-sized delivery vehicles, decreasing the number of vehicles in operation by facilitating the use of vehicles returning from their destinations, shortening the distance of transportation and delivery, promoting joint delivery, and optimizing the loading ratio by reviewing the frequency of transportation on each route.
*1: A consigner whose volume of freight transportation consigned to freight carriers (including in-house distribution) involved in its business activities is 30 million ton-kilometers or more
*2: Food Loglstics lntelligent Network
*3: Ajinomoto Co., Inc., Kagome Co., Ltd., the Nisshin OilliO Group, Ltd., Nisshin Foods Inc., House Foods Group Inc., and Mizkan Holdings Co., Ltd.
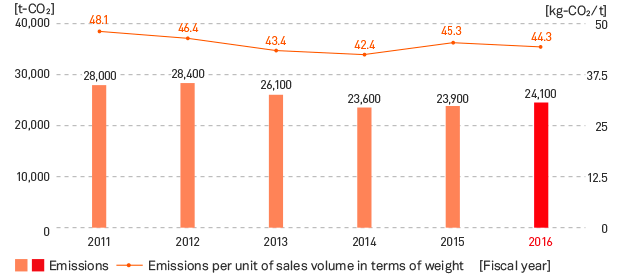
Modal Shift
The Kagome Group continues to make a modal shift to reduce the environmental load of its product transportation and delivery. A modal shift refers to a shift of transportation methods to those with a reduced a environmental load, such as rail.
As a result of these efforts, Kagome has obtained the Eco-Rail Mark certification from the Ministry of Land, Infrastructure and Transport of Japan, recognized as a company that uses railway transport proactively.
In addition, Kagome Tomato Ketchup, Kagome Sauce Worcester Jojuku, Kagome Sauce Chuno Jojuku, and Kagome Sauce Tonkatsu Jojuku obtained the Eco-Rail Mark Product certification in February 2014 under a program organized by the Ministry of Land, Infrastructure and Transport of Japan and the Railway Freight Association.
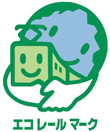
Joint Delivery
Kagome Group Companies in Japan carry out joint delivery with Mizkan Holdings Co., Ltd. and the Nisshin OilliO Group, Ltd., by loading products from the three companies on the same vehicle for their transportation.
In addition, joint delivery by six companies participating in the F-LINE project was commenced in the Hokkaido area in April 2016.
The objectives of joint delivery include a reduction in the environmental impact and tackling the shortage of truck drivers.
At present, the areas for the joint delivery account for 75% of the total area of Japan.
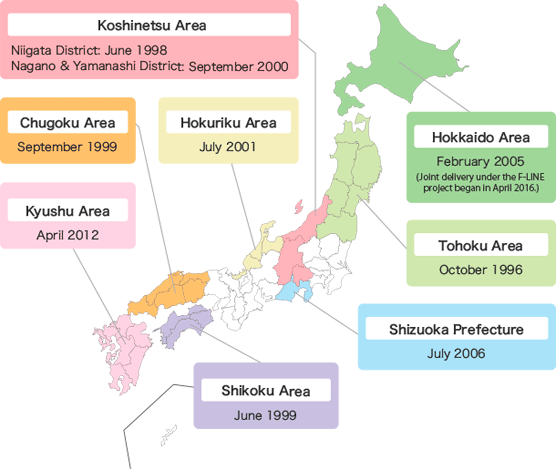
F-LINE
On February 2, 2015, six food manufacturers agreed to build a logistics platform for food companies (F-LINE) to establish an efficient, stable logistics system that contributes to the development of the overall food industry and the overall supply chain of the industry. Under this agreement, the companies are planning to build a sustainable logistics system.
The food industry faces many issues related to its logistics environment, including a shortage of truck drivers, rising distribution costs, and the necessity to take environmental measures such as reducing CO2 emissions. In response, the six food manufacturers are working to build a logistics platform for food companies, giving exhaustive consideration with a focus on (1) establishing a system for joint delivery by the six companies, (2) rebuilding a system for medium-distance trunk transport, and (3) standardizing logistics systems.
In April 2016, the first joint delivery (of shelf-stable products) by the six companies began to be operated in the Hokkaido area. At present, the six companies have a total of four delivery bases. For the joint delivery, these were consolidated into two bases, where products from the companies are stored and delivered together. This is aimed at improving the loading efficiency of each vehicle and the efficiency of logistics operations, including arrangements.
The joint delivery has allowed the six companies to reduce CO2 emissions. In the May-July period of 2016, total emissions by the six companies decreased by approx. 16% compared to the level before the commencement of the joint delivery.